Afisol Enterprise Resource Planning System (ERP)
Important of an Enterprise Resource Planning Software for Organization?
Enterprise Resource Planning (ERP) is an integrated software applications that standardizes and streamline the business processes across finance, human resources, purchasing, manufacturing, Sales management and other departments. Implementing an ERP system leads to streamline the flow of information and increase the efficiency of day -to-day operations by improving the productivity of employees and the reduction of operational expenses. ERP provides complete visibility of inventories movements, employee’s performance, material allocations and cash flow records.
Afisol Enterprise Resource Planning System (ERP)
Afisol Enterprise Resource Planning System (ERP) is a business process management software supports to simplify the managing of business operations. ERP software integrates all functions of an operation and access to data across accounting, human resource, supply chain management, Quality Assurance, project management, Inventories, Manufacturing and sales Orders in a single database with accurate details. System allows organizations to have an overview of the operations and convert data into information to make accurate management decisions.
Modules of Afisol ERP System
The purchasing module streamline the purchasing process of an organization and provides complete purchasing traceability. System enables to generate purchase requisitions based on created Material Requisitions. Users can request quotations from various suppliers referring to purchase requisitions. System provides the facility to upload quotations received from suppliers. The user will be able to raise a Purchase Order, refer to a quotation.
Purchase management module contains the following:
1.1. Supplier Registration
1.2. Request for Quotation
1.3. Purchase Quotation
1.4. Purchase Order
1.5. Purchase Order Approval
1.6. Supplier Invoice (Account payable invoice)
1.7. Purchase Quotation via RFQ
Raw material inventory module tracks the real time movement of the raw material inventories.
System handles raw material receiving, supplier returns, material requests, raw material issuing for production and returns. Users can create Material Requisitions. In case of stock imbalances, system facilitate for stock adjustments and inventory counting.
Finished goods inventory contains ready to sell finish goods of the company. System enables to set up bin locations with racks, stacks and shelves and manage order wise inventories. System records the finish goods IN and OUT, issue to repacking, goods issuing and dispatch. Managers are able to monitor order wise inventory, valuation, Inventory aging and expire dates to have real time overview of the inventories for accurate management decisions towards income generation.
Add on features: Barcodes, QR codes and RFID tags integrated with PDA devices and automated scanning devices.
The inventory module contains the followings:
2.1. Create Warehouse with Bin Card Location
2.2. Create Items
2.3. GRN
2.4. Material Requisition
2.5. Material Issue
2.6. Dispatch
2.7. Inventory Count and adjustments
2.8. Supplier Return
Production module enables user to manage and monitor the production process of the company. System passes information to the relevant departments such as Sales, Inventory, Purchasing, Quality, Production Planning and other departments to avoid miscommunications and streamline the production process. In each step of the process, management is able to monitor working progress, product quality, and the status of the production order. In end of each production, managers are able to calculate the yield, by-products, wastage and quality of the production to make proper management decisions.
Future Capacities: System has ability to link with an integrated production system (Smart Factory Module) with Barcodes, QR codes, RFID, PDA devices or any other relevant hardware devices to capture data.
The manufacturing management module contains the following:
3.1. Bill of Material (BOM)
3.2. Create Production Order
3.3. Production planning
3.4. Barcoding
3.5. Product Labeling
3.6. Box Labeling
3.7. Process Master
3.8. Consumption Details
3.9. Wastage and By-Products Details
3.10. Production Output and track working progress
3.11. Breakdown Details
QA module ensures the production performance and assist to match the output with the specified manufacturing standards to meet the requirements with minimal costs through streamlined processes. The quality control module provides, total control over all stages of production to enhance the production visibility and maintain standards such as ISO, FDA EU and BRC. User will be able to proceed quality inspection at any stage of the process. When sending a random samples of materials for the quality test, system enables user to record the results of quality parameters and upload documents related to quality inspections. Additionally, system provides the facility to ban or reduce raw materials due to quality issues. In case of using banned raw material at any stage, system will notify users through an alert.
The quality assurance module contains the following:
4.1. Set quality Parameters with bench marks
4.2. Create Quality Plans
4.3. Sample check
4.4. Approve or reject batch
4.5. Banned Raw materials
Maintenance module in ERP provides an integrated solution to support the operational needs of an enterprise-wide machineries and systems. The module includes features covering all aspects of plant/machine maintenance. By maintaining machines in optimum conditions, organization can reduce cost and carry out manufacturing efficiently while saving time of maintenance team.
A maintains management module contains the following:
5.1. Machine registration
5.2. Service Request/Breakdown request
5.3. Work order
5.4 Production down time reports
Sales module allows organization to track the sales process starting from taking sales lead to customer product dispatch. System allows to create the sales orders refer to the Purchase Order received from the customers. Users are able to review the previous orders made by the customers and the available quantity of required item. User is able to add item details such as product name, attributes, unit price, quantity, delivery details to the sales order. System facilitate users to view the status of the sales orders with delivery date and generate customer invoices.
Sales module contains the following features:
6.1. Customer Registration
6.2. Sales Lead
6.3. Sales Quotation
6.4. Create Sales Order
6.5. Create Customer Invoice
6.6. Sales Pending Quotation
6.7. Sales Quotation Cancellation
6.8. Customer Returns
The Finance and Accounting Module mainly aims to improving the wealth, profit margin, minimizing expenses, promoting savings, ensuring safety on investments and increasing the value of the organization. This Finance and account module in the ERP is one of the most sensitive modules which can be used to proper billing and accounts management.
Finance and account module contains the following sections:
7.1. Chart of Accounts and Ledger
7.2. Outgoing Payments
7.3. Incoming Payments
7.4. Banking Registration
7.5. Bank Reconciliation
7.6. Trial Balance Report (TB )
7.7. Balance Sheet
HR and Payroll module facilitates with employee registration and handle their salary payments.
Managers will able to keep records of division wise employee counts, shifts wise employee counts. Management is able to get the division wise employee costs calculations and employee details records at any instance. According to the attendance and their allowances, system will calculate payroll of the employees. System has ability to connect to finger print machines or card readers to retrieve attendance details and connects to manufacturing module to receive the performance to calculate incentives. Users has facility to generate necessary report to evaluate and submit to audits.
HR and payroll management module contains the following:
8.1. Organization Structure
8.2. Timesheet with Biometrics
8.3. Attendance Management
8.4. Payroll
Information technology department can be identify as a main part of a modern organization. System can manage users, alter permissions, manage work flows or change settings of the ERP.
Information technology module contains the following:
9.1. Create user groups
9.2. Add permission for user groups
9.3. Create users or deactivate users
9.4. Change settings of the ERP
9.5. Backup the database
9.6. View user logs
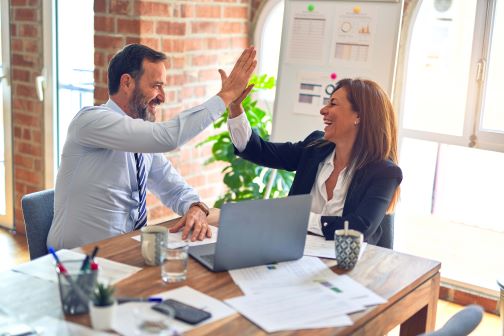
Benefits of the ERP System
- Facilitate for Facts Based Management Decisions
ERP system contribute with accurate and real time information thereby improving the quality and speed of decision making. - Improves the Accountability and Transparency
ERP connects with each and every department of the organization to maintain the information flow to keep link between the information. Thus, system helps to reduce the misleading information and human calculation errors by automating the information process. - Increased Productivity in business process
Due to the systematic information flow, most of the manual reporting and calculation time will be reducing. Most of the reports such as management reports, quality assurance report and packing list generations also can be handle through the software, By having redundant processes automated, employees can focus their efforts on more demanding tasks or employees have more time to work on other time sensitive, pressing projects and tasks. - Centralize information to Monitor Entire Business Process
ERP system ensures that all the information from different departments and processes are integrated into a single database. This improves the organization data accuracy, which eliminates making potential business mistakes with false data and analytics. Further it is easy to check the performance of different areas in the business process and identify the areas that are falling short. - Improved customer relationship
System facilitate with supplier registrations, evaluations and sales order management features to manage the customer base of the organization and to provide high quality customer service. Managers are able to keep records of the customer wise order details to monitor their buying patterns provide effective service. - Reduction of operational cost
With one source of accurate, real – time information, ERP solution reduces administrative and operational costs, allows businesses to utilize money in other, much needed areas. Further system helps to transform the business with growth challenges through formalization processes such as production planning, order processing and reduction of duplication of tasks. - Business Transformation
Structured ERP software enables the addition of new users and functions to grow the initially implemented solution over time. When a business is ready to grow and continue to build, enterprise resource planning software will aid in facilitating the growth.